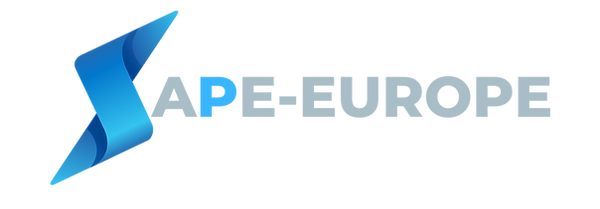
Search Results
4 results found with an empty search
- Progress in Power Transformers Applications in Australia's Mining and Tunnelling Industries
Introduction: Power transformers have long played an essential part in Australia's mining and tunnelling industries, providing reliable transmission of electrical energy efficiently and reliably. Technological developments and industry requirements have resulted in numerous advances for power transformers to ensure optimal performance, safety and sustainability - providing for peak performance at optimal cost and sustainability over the years. This article details their history within Australia's mining and tunnelling sectors while outlining key milestones that have changed Australia's landscape since their introduction. Early Beginnings: Australia's mining and tunnelling industry started out modestly; diesel generators provided electricity to equipment while further enhancing operations' scope and efficiency. But as operations expanded rapidly, more robust power solutions became essential. Power Transformers Revolutionise the Industry: Power transformers have transformed the industry by providing efficient transmission of electricity over long distances. Power transformers quickly became a mainstay in Australia's mining and tunnelling sectors during the mid-20th century, helping ensure a smooth flow from power stations to remote mining sites or tunnels with increased productivity while decreasing operational costs. Advances in Design and Efficiency: With industry expansion came power transformer manufacturers' efforts to enhance both design and efficiency of these essential components. One notable development was the oil-filled transformers' introduction, providing greater insulation and cooling properties enabling higher voltage levels while meeting performance and safety requirements. This innovation allowed transformers to operate safely at higher voltage levels while meeting performance standards while meeting all safety regulations. Adopting more advanced core materials, like amorphous metal alloys, significantly increased energy efficiency and decreased losses; these transformers greatly enhanced mining and tunnelling operations by providing a reliable power supply for heavy machinery and equipment. Integration of Monitoring and Protection Systems: With digital technologies' introduction into mining and tunnelling industries, power transformers became smarter and safer. Integrating advanced monitoring and protection systems allowed real-time tracking of temperature, oil level and load conditions; providing real-time information which allowed proactive maintenance aimed at avoiding transformer failure and optimising operational uptime. Talk to Australian Power Equipment about monitoring systems here. Renewable Energy Integration: Australian mining and tunnelling operations have increasingly prioritised sustainability by adopting solar and wind power to decrease their environmental footprint. Power transformers have played an essential part in this transformation by helping integrate renewable sources such as solar and wind into operations; advanced transformers equipped with grid-forming capabilities also facilitate seamless synchronization between renewable energies like these with existing power grids reducing fossil fuel reliance while contributing towards greener future. Safety and Compliance Standards: In the mining and tunnelling industries, safety has always been of utmost concern. Transformer manufacturers have developed power transformers to comply with stringent safety and compliance standards and implement fault detection. Australian Power Equipment is the agent for B&D transformers in Australia and can supply both new and in-stock refurbished transformers, specific to your needs. Speak to us at info@australianpowerequipment.com.au or view our new stock here and our ready to go In Stock here #powertransformers #australianpowerequipment #powerequipment #powertransformersaustralia
- B&D: Trusted supplier of Power Transformer, Distribution Transformers & Instrument Transformers
PT. Bambang Djaja, commonly known as B&D Transformer, stands as the premier manufacturer of Power, Distribution, and Instrument Transformers in Indonesia. With its establishment in 1985 in Surabaya, Indonesia, the company has consistently excelled by embracing the latest technology, employing cutting-edge machinery, and cultivating a team of highly-qualified professionals to meet the ever-growing demands for transformers both within Indonesia and on a global scale. A Trailblazer in Transformer Manufacturing In 2016, PT. Bambang Djaja proudly became the first "purely Indonesian" company to successfully manufacture 150 kV Power Transformers. Building on this milestone, the company is now actively developing transformers with ratings of up to 500 kV. This commitment to innovation and progress solidifies B&D Transformer's position as an industry leader Tailored Solutions for Site-Specific Requirements B&D Transformer understands that each customer possesses specific requirements, necessitating customised solutions. Rather than offering one-size-fits-all transformers, the company takes the time to engage with Australian Power Equipment, comprehensively understanding their needs and crafting tailored solutions to meet their specific transformer demands. Supported by sophisticated design software and state-of-the-art production facilities, B&D Transformer's engineers can seamlessly handle both large series production and small batch orders with quick re-tooling capabilities and Australian Power Equipment have confidence in their deliverables. A Focus on Research and Development Dedicated to consistently improving its products and services, B&D Transformer invests its resources into enhancing performance and staying at the forefront of the transformer industry. The company actively seeks out the latest developments in materials and production technologies, regularly upgrading its facilities to ensure optimal performance for #transformer manufacturing. By benchmarking against the best in the field, B&D Transformer continually strives to surpass expectations and deliver top-quality transformers to Australian Power Equipment. A Team of Dedicated Professionals At B&D Transformer, a team of talented, experienced, and dedicated personnel form the backbone of the company. Their accumulated knowledge serves as a treasure trove, constantly refreshed and supplemented to keep pace with transformer industry advancements. The company conducts regular internal training programs to ensure its workforce remains up-to-date with the latest transformer developments in the field. This commitment to continuous improvement guarantees that Australian Power Equipment receives the best transformer products and services available. Recognitions and Certifications B&D Transformer manufactures its products in adherence to renowned specifications such as IEC (International Electrotechnical Commission), ANSI (American National Standards Institute), NEMA (National Electrical Manufacturers Association), BSI (British Standards Institution), and SPLN (PLN Standard). To ensure the highest quality standards, the company routinely submits samples to independent laboratories for thorough testing in Indonesia and the surrounding region. Furthermore, PT. Bambang Djaja holds several certifications, including ISO 9001:2015, ISO 14001:2015, ISO 45001:2018, and SMK3 Kemnaker, demonstrating its commitment to quality, environmental responsibility, occupational health, and safety. B&D Transformer's products are certified by reputable organizations such as PLN PUSLITBANG, BP MIGAS, ASTA, and ATEX, further cementing their reliability and compliance with industry standards. Choose Australian Power Equipment's B&D Transformers for unparalleled transformers. When it comes to Power, Distribution, and Instrument Transformers, PT. Bambang Djaja (B&D Transformer) is the supplier you can trust. With a focus on tailored solutions, continuous research and development, a dedicated team of professionals, and a commitment to excellence, B&D Transformer consistently delivers exceptional products and services. Backed by numerous certifications and accolades, the company's transformers offer reliability, performance, and compliance with international standards. Choose B&D Transformer as your preferred supplier and experience the power of exceptional transformer solutions. SEE OUR B&D TRANSFORMERS OR see what B&D transformers we have IN STOCK ready to go #australianpowerequipment #transformersaustralia #powertransformers #distributiontransformers #newtransformers #secondhandtransformers
- Installing Mining Cables; Ensuring Secure and Reliable Connections
A well designed and properly installed electrical infrastructure is crucial for the safe and efficient operations of mines and tunnel excavations. There are various methods of installing mining cables, both on the surface and underground. From suspension and cleats to ducts and trenches, each installation method plays a significant role in ensuring the longevity and reliability of our mining cables through thought-out ease of installation for manual handling safety, ensuring relevant mechanical protection and standards compliance. A. Surface Installations a. Suspension: mining cables can be suspended using our CAB cable management products from centenary wires or wall hooks. This method is suitable for areas where the cable needs to be elevated. See our CAB cable management products here b. Cleats: Cleat fixing is used when the cable runs along the side of a building and cleats securely hold the cable in place. c. Ducts: for cables installed along a designated path, a duct is created by digging a trench and utilising precast concrete segments. Brackets or cleats fasten the cable to the duct’s walls ensuring a stable and protected installation. Additional spacing can be undertaken via cable tray and supports to ensure spacing and ventilation. d. Wall Brackets: Inside buildings cables can be secured to walls with brackets bolted to the wall to provide damage to cables. e. Trench: when burying cables, a cable trench of adequate depth is excavated considering the operating voltage and site conditions. The cable is placed on a bed of sand and covered with additional sand. Interlocking cable tiles are placed on top to provide continuous cover, followed by a layer of earth. Marker posts are erected to indicate the cable trench route. f. Shaft installation: Vertical cable installation in a shaft involves clamping the cable at regular intervals using wooden cleats. The cleats are bored individually to fit the cable securely, ensuring a firm grip. B. Lowering the Cable – Single point Suspension and standard cable installation In shaft installations, cables are typically lowered into the shaft using a drum-mounted system or runway system depending on cable weight and length of run. Cables that can be secured within the winder shaft can be secured within the cage. As the cage descends, the cable is laid out and anchored at the shaft top. An alternative method involves lashing the cable to an engineered design utilising wire suspension ropes. C. Underground Installations In underground mining, cable installations near the pit bottom may utilise cleats on brackets or cable hangers to secure cables to walls. In roadways and gate roads, cables are commonly suspended from the roof or rib bolt bars or arches. Maintaining slackness in the cable is crucial to accommodate roof movements and prevent strain. Australian Power Equipment provides mining cables to Australian mining standards in various lengths and widths to suit different requirements. See NEW PRODUCT CABLES here Australian Power Equipment also can provide cable management solutions via their CAB cable hangar products. Proper installation of mining cables is vital for maintaining a reliable and secure electrical infrastructure in mines. Whether on the surface or underground, selecting the appropriate installation method ensures the longevity of mining cables and minimises the risk of damage. By adhering to best practices and considering the specific conditions of each mine, mining operations can enjoy uninterrupted power supply and enhance overall safety and efficiency. Contact Australian Power Equipment for your cable management needs at www.australianpowerequipment.com.au or info@australianpowerequipment.com.au #miningcables #australianpowerequipment #cables #solarhangers #cablemanagement #cableinstallation
- Power Distribution in Mines; Ensuring Safe, Robust Electrical Infrastructure with Mining Cables.
At Australian Power Equipment, we are asked a lot about Mining Cables for use in Australia. In any mining operation, whether underground or at the surface, electricity plays a crucial role in powering various equipment and systems. The electrical power required is typically sourced from either an island generating station at the mining operation or, more commonly, from the local electricity network through a primary substation with an IT earthing system. Australian Power Equipment supplies new and refurbished switchgear and transformers for these substations, to many mines throughout Australia. See our new cables here See our refurbished cables here It is essential to establish a robust power distribution infrastructure to ensure uninterrupted operations and promote efficient resource production. That’s where Australian Power Equipment mining cables that conform to Australian Standard AS 2802 Electric cables, have their role in powering mining equipment. Mines require various cables; 1. Mining Cables; Robust for Challenging Conditions Cables used in Surface and underground collieries face harsh and demanding conditions, such as roof and rib falls, standing water both on the surface and underground, fly rock and other potential causes of damage. Mining cables need to be robustly constructed to withstand the harsh environment and treatment they can receive. Furthermore, regular maintenance is essential to ensure the safety and reliability of these cables. Australian Power Equipment provides mining cables and operational strategies that ensure the reliability and durability of mining cables that are paramount for efficient resource production. 2. Distribution Cables; Evolution and Usage in Mines In current mining operations, PVC/XLPE and LSOH insulated cables with metric dimensions are predominantly used for medium and low-voltage distribution applications. Prior to the introduction of XLPE technology paper insulated Lead sheath Steel Wire Armoured cables, PILSWA ( Metric and imperial sized) were common and are still in use today. The previous PILSWA cables were robust in design however have a significantly lower current carrying capacity AND production of Lead Sheathed cables has decreased. Cables to 2802 are available primarily in three core + 3 earth+ pilot configurations with three-core cables being the norm for three-phase AC distribution systems on an IT earthed system with 5amp earth fault limitation utilising quick-release receptacles. 3. Cable Construction and Features. The conductors of mining cables are typically laid up together in a spiral arrangement. The cores can consist of multi-stranded tinned copper semi-conductor layering insulated with R-EP-90. Any gaps between the mining cable conductors and central pilot core are filled with a semiconductor cradle to achieve a uniform circular section covered with an open weave braid and overall covered by heavy-duty elastomer outer sheath. Mining cables are available in semi-conductor screened, 241 and both single-armoured and double-armoured types. The armour layers, consisting of galvanised steel wires spirally laid along the cable, serve as mechanical protection. Double-armoured cables employ a separator of compounded fibrous tape between the two armour layers, with the galvanised wires spiralled in opposite directions. As the agent for Untel, Australian Power Equipment provides solutions to cable mining requirements in Australia. A reliable and robust electrical infrastructure is crucial for the efficient operation of mines. Mining cables play a vital role in ensuring the safe and uninterrupted distribution of electrical power in challenging mining environments. The industry has seen a shift in medium voltage cables from traditional paper insulated cables PILSWA to modern PVC/XLPSWA insulated cables which offer improved performance and longevity. Australian Power Equipment have XLPE cables In Stock. Regular maintenance and adherence to earthing systems and regulations are essential for the safety and reliability of mining cables and personnel. By prioritising the quality and durability of power distribution systems, mines can optimise their operations and enhance coal production efficiency. Contact Australian Power Equipment for your cable management needs at www.australianpowerequipment.com.au or info@australianpowerequipment.com.au #miningcables #australianpowerequipment #powerequipmentaustralia #tunnellingcables #untelcables #untel